APH Behind the Scenes: Production Improvements
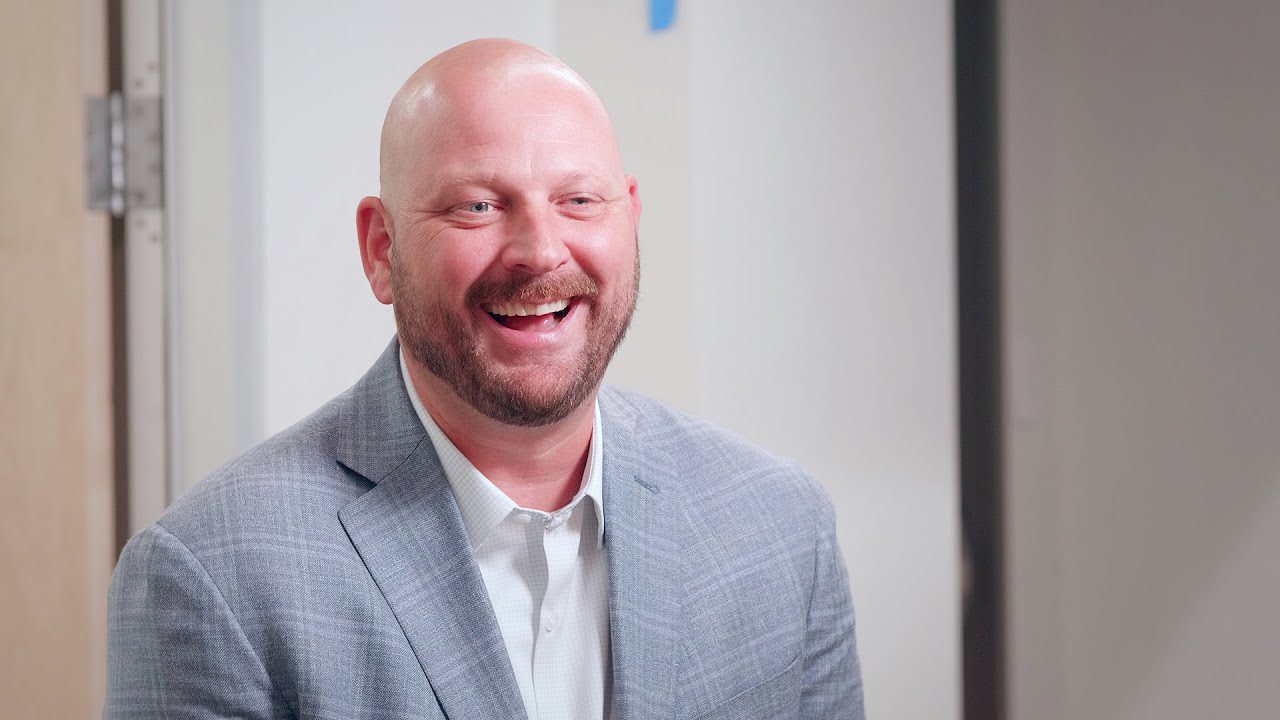
APH’s production team is responsible for making innovative products for our customers. Wayne Price, Vice President of Production and Logistics; Andrew Mouton, Director of Technical and Manufacturing Research; and Jo Holt, Operations Engineering Planning Manager, discussed how the team is working to streamline manufacturing processes.
Production Improvements
The production team has made many changes on the production floor to improve efficiency and product design, giving APH the ability to create higher-quality products and sell them at lower prices.
One new development on the production floor is the capability of printing onto plastic with the Ricoh printers. The faster process creates a higher resolution of print and helps to better maintain APH’s registration. Next, the team can now bring in outsourced, subcontracted product parts. “We took what was a 30 to 90 day lead time for these parts and reduced that down to two to three days,” said Jo Holt.
Andrew Moulton said, “Using our thermotype machines to emboss braille and tactiles onto a variety of different media allows us to streamline the process. These are very fast machines, so what used to take maybe a week or a few weeks to print and emboss, we have down to days now.”
Additionally, the shop floor has been redesigned so there is no waste in movement. We worked with vendors to enhance the way we interact and to discuss how APH can use their machines in a way that is different from how they were designed to be used. The suppliers have also given APH tips on machine settings and ideas on how to better design tools to achieve desired results.
With these improvements, the production floor has seen significant changes in efficiency. Instead of creating 12 sheets per hour on a flatbed, the team can now run thousands of sheets per hour on the thermotype machines and can cut 4,000 an hour per machine. These processes can also be combined. For example, the team can print something on the Ricoh printers, bring it over to the thermotype embossers, emboss it, and even kiss-cut the parts. Rather than sending the Feel ‘n Peel Stickers to be produced with two outside suppliers, which would take months, APH can make them in-house in a few days. Other products whose production time has been reduced include the Classroom Calendar Kit (English and Spanish Editions), the ReadWrite Stand Mini, and Familiar Object Pictures. Andrew said, “That translates to lower costs for the customer and Quota dollars being spread further across APH products, giving APH’s customers more buying power.”
Learn more about production improvements by watching the video Creating a Culture of Innovation.
Share this article.
Related articles
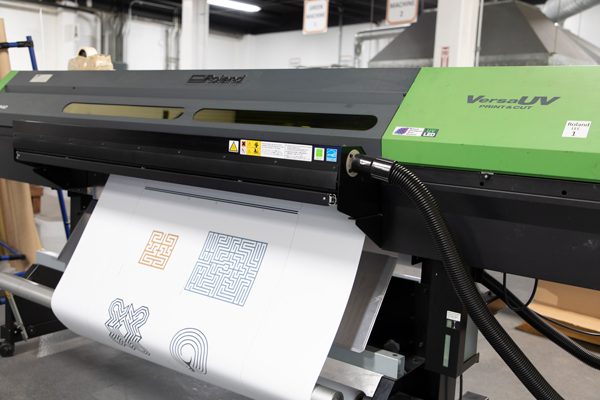
Switch to Using the Roland in Production Department Streamlines Processes and Creates High-Quality Graphics
For the past year, APH’s production department has been focusing on improving efficiency within the department. Thanks to the efforts...
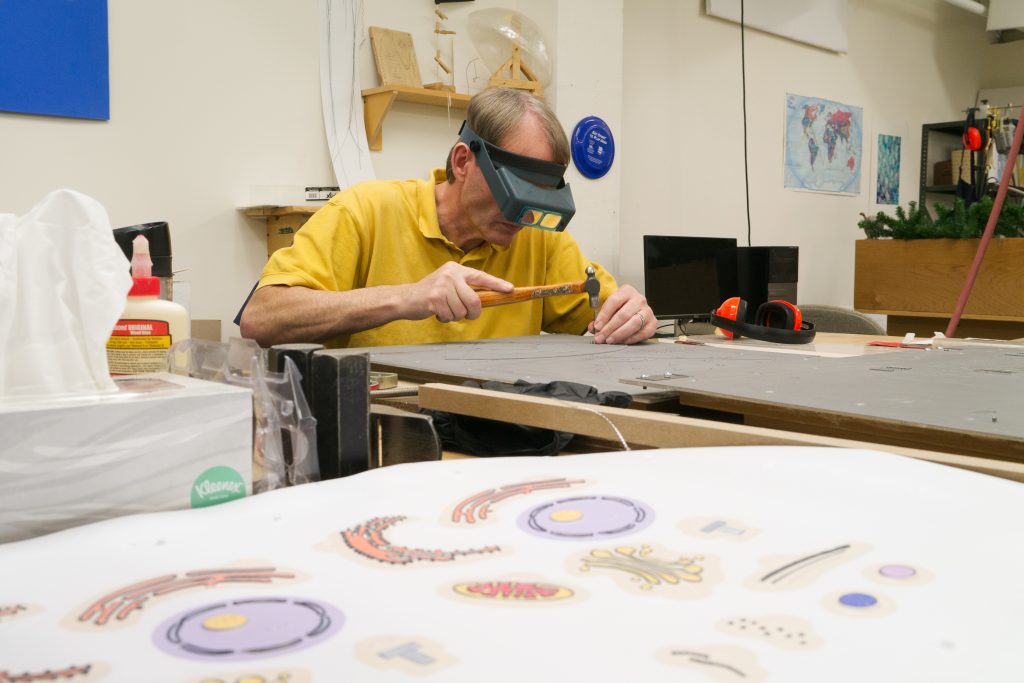
APH Behind the Scenes: The Model Shop
At APH, we’re always looking for ways to create new tactile graphics for our consumers, and our Model Shop is...
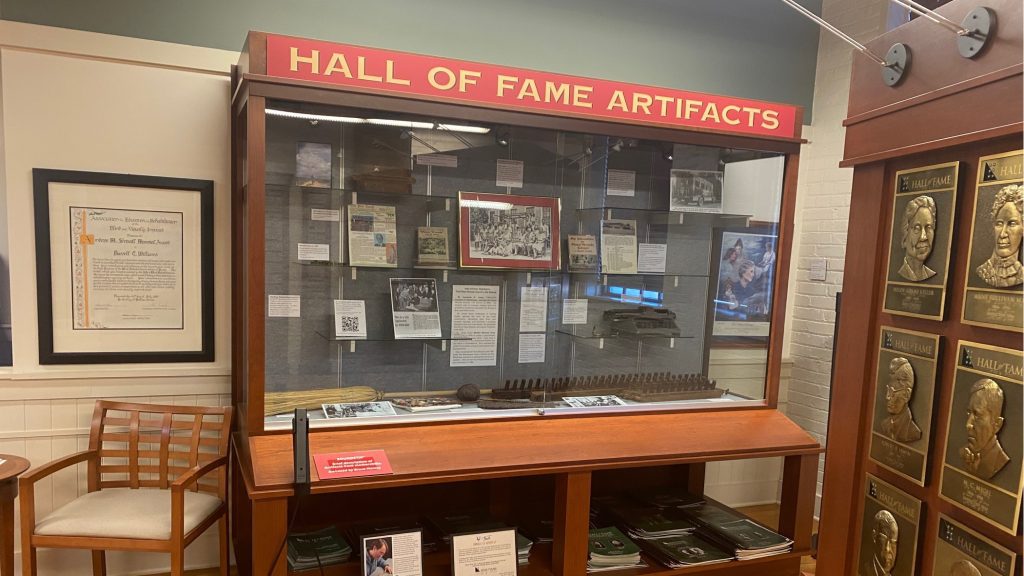
Lessons in Labels
In my nearly 20-year career in the museum field, I have been a part of an exhibit team, helped locate...